
Первый национальный химический дистрибьютор — компания «Русхимсеть» — построила систему автоматизации складских процессов
Отрасль : Химия, нефтехимия. Торговля. Транспорт и логистика.
Исполнитель: 1С:Первый Бит, Москва – Центральный офис
Функциональная область: Управление логистикой и складом.
29.04.2021 - 05.11.2021
Центральный федеральный округ РФ
Компания «Русхимсеть» построила систему автоматизации складских процессов на базе решения «1С:WMS Логистика. Управление складом», ред. 5.0. Особенности проекта были обусловлены необходимостью автоматизации процессов хранения в сложно организованном пространстве, с учетом специфики производимой заказчиком химической продукции, в максимально сжатые сроки. В результате проекта автоматизированы процессы приемки, размещения, хранения, отбора, отгрузки, инвентаризации продукции, обеспечено оптимальное размещение и хранение производимой продукции, в том числе опасных химических веществ.
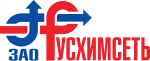
Цели проекта:
- Оперативная организация системы автоматизации складских процессов в новом комплексе с учетом особенностей хранения специфической химической продукции.
- Повышение прозрачности товародвижения внутри склада.
- Автоматизация рутинных операций ввода информации в систему.
- Повышение достоверности учетных данных по складским остаткам.
- Обеспечение двустороннего обмена данными с корпоративной учетной системой.
- Возможность масштабирования и тиражирования системы на филиальную сеть.
Для достижения этих целей проектной команде предстояло решить следующие задачи:
- Проработка процессов склада от поступления товаров на склад до отгрузки конечным клиентам, методическое обеспечение и реализация специфических особенностей учета и управления в системе автоматизации.
- Организация оперативной фиксации всех операций, связанных с перемещением ТМЦ в рамках склада для организации полноценного адресного хранения и обеспечения оперативного размещения, поиска, сбора и отгрузки продукции.
- Внесение типовых операций в систему посредством распознавания информации со штрихкодов с применением терминалов сбора данных (ТСД) (отказ от использования бумажных носителей, перевод всех сотрудников склада на работу с ТСД).
- Снижение количества расхождений учетных данных и фактических данных по остаткам.
- Настройка обмена между системами согласно требованиям.
- Создание архитектуры системы, которая предусматривает возможность подключения новых объектов автоматизации путем добавления новых настроек с сохранением действующих бизнес-процессов и интеграционных связей.

До старта проекта у компании было 2 автоматизированных ранее склада на базе. предыдущей редакции программного продукта («1С:WMS Логистика. Управление складом», редакция 4.х). Однако площади одного из складов уже не отвечали объемам производимой продукции и не позволяли обеспечить надлежащее хранение продукции с учетом соблюдения специфических правил товарного соседства сухой и жидкой химической продукции, опасных, токсических веществ. Для решения проблемы недостатка складских площадей был спроектирован и построен новый складской комплекс, оснащенный необходимым стеллажным оборудованием и техникой.
Существующая система на этапе переезда в новый складской комплекс и старта проекта не отвечала потребностям бизнеса в части обеспечения необходимой скорости выполнения операций сотрудниками склада. Поэтому было приянто решение оперативно организовать систему автоматизации складских процессов в новом комплексе с помощью решения «1С:WMS Логистика. Управление складом», ред. 5.0.
Система автоматизации складских процессов построена на базе «1С:WMS Логистика. Управление складом», ред. 5.0.
Схема архитектуры
Масштаб проекта:
- общее количество автоматизированных рабочих мест: 25;
- терминалов сбора данных: 20;
- вариант работы: клиент-серверный (сервер базы данных: Microsoft SQL Server), тонкий клиент, веб-клиент;
- среднее количество одновременно работающих пользователей — тонкий клиент: 10, веб-клиент: 12;
- общий объем складского комплекса составляет более 40 000 кв.м., склад является одним из самых высоких в Российской Федерации (хранение в 12 ярусов, высота верхнего яруса 18 м);
- склад состоит из одного помещения напольного и стеллажного хранения и двух помещений мезонина;
- склад разделен на несколько функциональных зон по параметрам класса опасности и по ABC-XYZ классификации номенклатуры;
- мощность нового склада составляет более 100 000 паллет в месяц;
- 31 рабочий поток;
- среднее число вводимых документов в день: 200-250;
- среднее число строк в одном документе: 15;
- количество номенклатурных позиций: 12 000.
В силу специфики бизнеса и необходимости оперативного управления большими потоками номенклатуры существовала необходимость автоматизации и использования современных ИТ-систем.
Особенности проекта были обусловлены организацией системы автоматизации процессов хранения в сложно организованном пространстве с 2 помещениями мезонина, с учетом специфики производимой компанией химической продукции, в максимально сжатые сроки. Был необходим срочный переезд склада, в связи с этим самым главным в ходе реализации проекта стало требование в обеспечении срочности запуска системы, товары начали поступать на склад уже на 2 этапе проекта.
Кроме того, уникальность проекта была обусловлена и некоторыми специфическими особенностями топологии складского комплекса. Общий объем складского комплекса — более 40 000 кв.м., помещение является одним из самых высоких (12 ярусов) в РФ. В ходе проекта необходимо было обеспечить соблюдение особенных правил товарного соседства опасных, горючих и токсических веществ, легковоспламеняющихся жидкостей, горючих жидкостей, едких, коррозионных веществ, пищевой и косметической химии. Было реализовано распределение потоков через точки передачи, в результате чего теперь штабелер в зоне стеллажного хранения снимает продукцию со стеллажей, оставляет в точке передачи в транзитной зоне с соблюдением соответствия проездов и стеллажей, а затем погрузчик подбирает и везёт в отбор.
Реализован функционал бригадного выполнения задач, реализован расчет сдельной оплаты труда сотрудников.
Реализовано распределение ТМЦ по высоте яруса.
В результате проекта в сжатые сроки реализован и введен в эксплуатацию современный, эффективный, масштабируемый инструмент автоматизации оперативного учета движения материальных ценностей в новом комплексе с учетом особенностей хранения специфической химической продукции и сложной организации помещения:
- Отлажены все логистические бизнес-процессы под реалии нового объекта.
- В результате внедрения WMS-системы, управление складом происходит в режиме реального времени, что позволило повысить прозрачность товародвижения.
- Обеспечены двусторонние обмены данными с корпоративной учетной системой.
- К системе подключены и введены в работу 20 ТСД.
- Автоматизированы рутинные операции ввода информации в систему: внесение типовых операций в систему посредством распознавания информации со штрихкодов с применением ТСД (отказ от использования бумажных носителей, перевод всех сотрудников склада на работу с ТСД).
- Благодаря автоматизации оптимизированы потоки сборки заказов и отгрузок, время на обработку входящего и исходящего потоков продукции существенно сокращено, в том числе за счет оптимизации маршрутов обхода при сборке заказа, устранения пустых пробегов.
- Повышение достоверности учетных данных по складским остаткам: снижение количества расхождений учетных данных и фактических данных по остаткам.
- Весь персонал склада обучен работе в системе, что позволило повысить точность и качество выполнения внутрискладских операций.
- Пользователи всегда имеют актуальную информацию о складских остатках в режиме онлайн.
Экономический эффект от внедрения:
- сокращение трудозатрат в подразделениях: 20%;
- ускорение получения управленческой отчетности: 20%;
- ускорение обработки заказов: 25%;
- рост оборачиваемости складских запасов: 30%;
- увеличение объема выпускаемой продукции / оказываемых услуг: 10%;
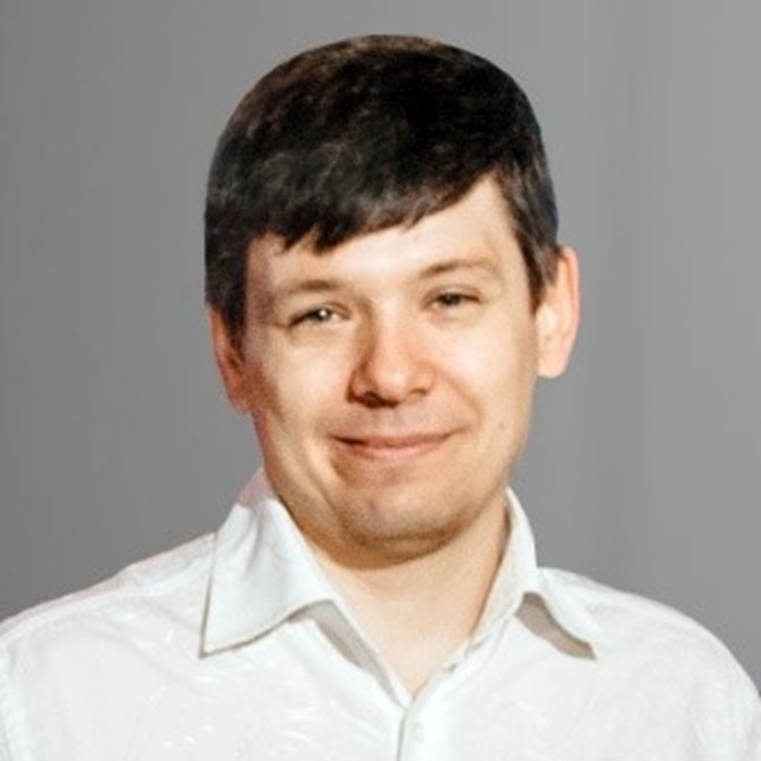
Дмитрий Гончаров
Главный системный администратор компании «Русхимсеть»В результате проекта мы имеем систему, которая позволила не только повысить качество, оперативность и прозрачность учета, но и в будущем тиражировать ее на всю нашу региональную сеть. Проект позволил организовать единое информационное пространство посредством обменов с корпоративной учетной системой и отладить работу всех пользователей. Автоматизация обеспечила оптимальную организацию складских процессов нашего комплекса, ускорила работу сотрудников склада и повысила прозрачность товародвижения.