
На заводе имени Козицкого построили комплексную систему управления производством
Отрасль : Машиностроение, приборостроение.
Исполнитель: Диалог Информационные Технологии
Функциональная область: Управление финансами. Управление закупками (МТО). Управление инженерными данными. Управление производством. Управление нормативно-справочной информацией.
07.04.2017 - 15.10.2017
Северо-Западный федеральный округ РФ
На заводе имени Козицкого построили комплексную систему управления производством и конструкторско-технологической подготовкой. Внедренная комплексная система реализована на базе решения «1С:Управление производственным предприятием» и функционирует в рамках нескольких юридических лиц. Уникальность проекта заключается в том, что выпускаемые заводом изделия имеют до семи уровней вложенности, содержат около тысячи изготавливаемых деталей, сотни материалов и комплектующих. После запуска проекта объем незавершенного производства снизился на 20%, а расчет плановой себестоимости, рентабельности заказов ускорился на 15%.
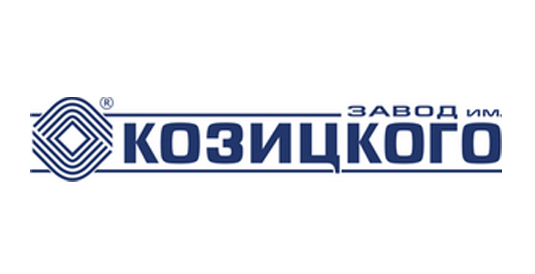
Завод им. Козицкого – это одно из старейших предприятий в России в области техники связи и телекоммуникаций. Сегодня это многопрофильное производственное предприятие, занимающееся созданием техники специального применения для Министерства Обороны, разработкой телекоммуникационного оборудования и оказанием производственных услуг. Входит в состав Промышленно-коммерческой группы «Радуга».
Цели проекта:
- Создание комплексной автоматизированной системы, отвечающей требованиям методологии ERP.
- Повышение эффективности и управляемости предприятием.
- Консолидация результатов хозяйственной деятельности по восьми юридическим лицам.
Задачи проекта:
- Ведение конструкторских и технологических спецификаций, определяющих состав производимых изделий, а также материальные ресурсы и операции, необходимые для их изготовления.
- Регламентация всех участников бизнес-процессов предприятия.
- Автоматизация процесса бюджетирования.
- Построение автоматизированной системы управления закупками и запасами.
- Автоматизация калькуляции цен на военную продукцию, плановой и фактической себестоимости продукции.
- Построение системы планирования потребностей в производственных мощностях и персонале.
- Планирование потребностей в материалах и комплектующих с учетом сроков поставок и складских остатков для выполнения плана производства продукции.
Предыдущая информационная система завода представляла собой лоскутную структуру из нескольких, не связанных между собой, учетных систем. Система управления производством собственной разработки была реализована на базе устаревшей платформы, материальный учет велся вручную, конструкторы и технологи работали в разрозненных системах. В результате перед заводом остро встал вопрос о модернизации информационной системы управления.
Проект реализован на базе решений «1С: Управление производственным предприятием 8» и «1C:PDM Управление инженерными данными». Решение имеет следующие развитые блоки:
- производственный учет,
- управление продажами и закупками,
- планирование,
- бюджетирование и финансовый учет,
- расчет управленческой заработной платы.
Для хранения и разработки конструкторской и технологической документации используется программный продукт «1C:PDM Управление инженерными данными». Теперь данные об утвержденных спецификациях (составе изделия) и технологии можно перенести в основную учетную систему в соответствующие объекты и отредактировать для целей производственного учета.
В процессе работ проведена интеграция программных продуктов «1С:Управление производственным предприятием» с «1C:PDM Управление инженерными данными» и «1С:Бухгалтерией 8».
В результате проекта автоматизировано 100 рабочих мест.
Прикладная архитектура системы
В будущем, планируется внедрение подсистемы оперативного планирования производства.
Выпускаемые заводом изделия имеют до семи уровней вложенности, содержат около тысячи изготавливаемых деталей, сотни материалов и комплектующих. Комплексная автоматизированная система дает возможность отслеживать процесс изготовления каждой детали с точностью до технологической операции на больших объемах данных и контролировать процессы обеспечения и комплектации конкретных сборочных единиц.
Процесс управления производством осложнялся тем обстоятельством, что процессы закупки и производства изделия могут начинаться до завершения процесса подготовки конструкторско-технологической документации, и необходимо учитывать соответствующие изменения нормативно-справочной информации (НСИ). Дополнительные требования выдвигались к процессам входного контроля закупаемых комплектующих изделий.
Качественные результаты проекта:
- снизилось время простоев или невыполнения заказов из-за нехватки материалов (за счет внедрения системы планирования закупок);
- сократилось время на регистрацию и обработку учетной информации, информация стала оперативной за счет объединения разрозненных блоков (конструкторская документация, программы производственного учета, автоматизация склада материалов) в одну учетную схему, использующую общие источники данных;
- снизился риск ошибок в принятии управленческих решений за счет оперативного доступа к актуальной информации, возможности сопоставления с плановыми показателями
- появилась возможность оперативно отслеживать исполнение производственного цикла и реагировать при смещении сроков выполнения заказов.
Ключевые количественные результаты проекта:
- процесс разработки и подготовки конструкторской и технологической документации для производства ускорился на 20%;
- объем незавершенного производства снизился на 20%;
- плановая себестоимость и рентабельность заказов рассчитывается на 15% быстрее;
- время на регистрацию и обработку учетной информации сократилось на 30%.