
Компания «Цикл» повысила управляемость производством на всех его стадиях и снизила производственные запасы на 30%
Отрасль : Пищевая промышленность и ТНП.
Исполнитель: ИТРП
Функциональная область: Управление производством.
04.01.2016 - 25.08.2017
Центральный федеральный округ РФ
Фирма «Цикл» столкнулась с рядом проблем, свойственных растущему предприятию — наращивание производственных мощностей требовало построения эффективной системы производственного планирования и управления. Для решения поставленных задач было принято решение повысить качество и снизить трудоёмкость всех бизнес-процессов с помощью системы «1С:ERP Управление предприятием». В ходе проекта была пересмотрена методология планирования производства, а также процессы формирования сменно-суточных заданий, обеспечения производства комплектующими и материалами, учёта хода производства и списания затрат. Предприятие перешло к учёту всех единиц нашей продукции в режиме реального времени. В результате удалось улучшить управляемость и запасами, и производством в целом, повысить точность и эффективность как планирования производства, так и учёта продукции, материалов и полуфабрикатов.
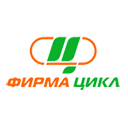
Фирма «Цикл» — российский производитель садовых и хозяйственных товаров из пластика. Это предприятие полного цикла: от разработки нового изделия до выпуска его на рынок. Ассортимент продукции предприятия насчитывает 200 наименований в трех категориях: садовые, хозяйственные и спортивные товары. В 2016 году введен в строй новый завод, который увеличил мощности предприятия в 2,5 раза (более 5 миллионов единиц продукции в год), а также большой логистический центр на 4000 «паллетомест». Количество сотрудников — около 250 чел.
Цель проекта — сокращение уровня затрат на производство и снижение себестоимости выпускаемой продукции.
Задачи проекта:
- Автоматизировать процесс планирования производства.
- Обеспечить равномерную нагрузку на производство.
- Выстроить процесс учета хода производства и повысить управляемость производства.
- Обеспечить точность и актуальность информации о запасах тмц в производстве и на складах.
- Сократить незавершенное производство.
- Оптимизировать производственные запасы.
- Ускорить выпуск готовой продукции.
Вследствие кризиса два года назад с рынка ушёл главный конкурент «Цикла» — китайские производители. При этом на предприятии в 2016 году ввели новые производственные мощности. Это привело к росту продаж и объемов производства. Строительство нового производственного и складского корпусов позволило увеличить объемы производства в 2,5 раза.
Однако это сказалось на оперативном планировании производства продукции: стали срываться поставки, возникла неразбериха со складами — не знали точно, где и что лежит. «Требовалось собрать воедино и усовершенствовать весь производственный функционал, а также снизить ручной труд по планированию и повысить управляемость производством», — рассказывает Ирина Хлупнова, руководитель ИТ-проектов предприятия «Цикл».
Проблема осложнялась тем, что до внедрения «1С:ERP Управление предприятием 2» на заводе использовалась система «1С: Управление производственным предприятием 8». Она была серьезно переработана, содержала в себе много нетипового функционала, в том числе функционала планирования производства, который, по сути, заключался в ручном планировании. Ручным составлением планов, сменных заданий занимался отдел планирования. При этом в программе практически отсутствовал учет хода производства — фактически, на произведенную продукцию просто списывались материалы, раз в месяц проводилась инвентаризация, по которой выверялись остатки.
Владелец компании и топ-менеджмент поставили следующие задачи:
- сократить незавершенное производство;
- оптимизировать производственные запасы;
- ускорить выпуск готовой продукции;
- обеспечить равномерную нагрузку на производство.
Для решения этих задач была выбрана новая система — «1С: ERP Управление предприятием 2» (на тот момент была бета-версия системы).
В системе «1С:ERP Управление предприятием 2» работают следующие блоки:
- управление продажами;
- управление закупками;
- управление запасами в связке с системой «1С:WMS Логистика. Управление складом»;
- планирование продаж и планирование производства;
- планирование закупок;
- управление нормативно-справочной информацией;
- расчёт себестоимости;
- управление ремонтами оборудования.
«Мой подход был — минимум доработок, максимум типового решения, чтобы стоимость владения системой была оптимальной. Если понадобятся доработки, то они должны быть внешними и не затрагивать типовое решение», — уточняет Ирина Хлупнова. Тем не менее, во время проекта пришлось провести ряд доработок типового решения.
- Реализовано автоматизированное рабочее место (АРМ) операторов, которое стоит на шести терминалах в цеху. Появление первичной информации в системе идет непосредственно от первоисточника — конкретного сотрудника. Каждый выпускающий продукцию работник должен сам отчитаться за то, что он сделал, какие работы выполнил.
- Создано АРМ закрытия смены.
- Введено АРМ формирования расписаний и графиков для планового отдела.
- Разработан документ «План остатков», которым пользуется плановый отдел и отдел продаж. Общее число пользователей системы «1С:ERP Управление предприятием 2» приближается к 80. В системе работает порядка десяти инженерно-технических работников производства.
Исторически учёт материалов и полуфабрикатов велся по факту выпуска изделий, все списания на расход оформлялись по нормам, без учета отклонений от реального потребления. Постоянно выполнялись корректировки остатков, что требовало дополнительных трудозатрат на проведение инвентаризаций. Сейчас мы перешли к нормальному учету всех единиц нашей продукции в режиме реального времени в системе класса ERP. Это было нелегко, к этому не привыкли, сложности есть до сих пор. Но, по крайней мере, сейчас можно уверенно говорить — где, что и в каком количестве у нас есть.
В первую очередь была пересмотрена методология планирования производства — существующая система формирования производственных заказов под ожидаемый расход была изменена на систему планирования производства продукции и полуфабрикатов под страховой запас. Для реализации подсистемы оперативного планирования и расчета графиков производства была настроена новая модель нормативно-справочной информации, включающая в себя данные о продукции, схемах обеспечения, рабочих центрах и нормах выполнения операций.
Также пересмотрены процессы формирования сменно-суточных заданий, обеспечения производства комплектующими и материалами, учета хода производства и списания затрат. Разработаны автоматизированные рабочие места с использованием средств штрих-кодирования, которые позволили получать информацию о выпуске и движении всех полуфабрикатов и продукции в производстве практически в режиме онлайн. Предприятие ушло от «фиктивного» учета материалов и полуфабрикатов.
Новая методология планирования производства
На предприятии полностью поменяли систему планирования производства, причем не только в части выполнения расчетов, но и в части самой методологии. До внедрения системы «1С:ERP Управление предприятием 2» планирование сводилось к «ручному» прогнозу: что нам нужно произвести, чтобы выполнить планы продаж. Это приводило к затовариванию складов, к излишкам полуфабрикатов, которые негде было хранить.
С внедрением «1С:ERP Управление предприятием 2» перешли на методологию планирования под страховой запас. Причём как под страховой запас готовой продукции, так и под страховой запас полуфабрикатов собственного производства.
На предприятии ограниченный парк оборудования: порядка 45 термопластических станков, на которых выпускается 700–800 позиций деталей, которые нужно периодически переставлять и дозагружать оборудование. И требуется очень тонкая балансировка оборудования, чтобы выпустить всю ту линейку номенклатуры, которая продается в течение одного сезона. Эту балансировку решено было выполнять не на этапе оперативного планирования и расчета внутрицеховых планов, а на этапе объемного планирования производства продукции. Был разработан документ «План остатков», позволяющий управлять уровнем страховых запасов в зависимости от изменения уровня спроса на продукцию. И, соответственно, именно этим документом выравнивается и балансируется производство, обеспечивается равномерная загрузка оборудования на протяжении всех месяцев сезона. Благодаря «плану остатков» оборудование деталями загружается равномерно.
Для полуфабрикатов собственного производства выбрана экспертная оценка уровня страховых запасов, но и ее считали в зависимости от уровня страховых запасов готовой продукции. Обеспечиваются запасы, которые позволяют работать два дня без сбоев. Как только двухдневный запас заканчивается, система сигнализирует о необходимости пополнения.
«Новая методология планирования очень хорошо себя показала в промышленной эксплуатации. Благодаря ей мы избавились от множества проблем: перезатоваривания складов и высоких запасов. И, что очень важно, мы получили управляемость и гибкость при производстве – теперь при переходе на продукцию к новому сезону мы не имеем массы полуфабрикатов, которые у нас накапливались прежде», – разъясняет Ирина Хлупнова.
«В результате мы смогли улучшить управляемость и запасами, и производством в целом, повысить точность и эффективность как планирования производства, так и учета продукции, материалов и полуфабрикатов», — резюмирует Ирина Хлупнова. С помощью системы маркируется вся выпускаемая продукция. Маркировка содержит информацию о том, кто когда, в каком количестве выпустил продукцию. Это позволяет найти работника, допустившего брак при получении рекламации от клиента.
Количественные результаты проекта:
- снижение запасов собственного производства на складах — 30%;
- рост эффективности труда ИТР и служащих — 20%;
- повышение точности планирования — 60%;
- снижение уровня незавершенного производства —20%;
- сокращение времени на планирование — 60%;
- повышение точности учета хода производства — не менее 80%.
Полная окупаемость проекта будет понятна, когда на предприятии будет внедрен функционал финансового планирования и бюджетирования. Тогда можно будет посчитать, как с помощью системы фирма «Цикл» экономит деньги. На сегодняшний момент, за счет сокращения складских запасов и повышения точности учета хода производства, проект окупился на 40%, считает Ирина Хлупнова.
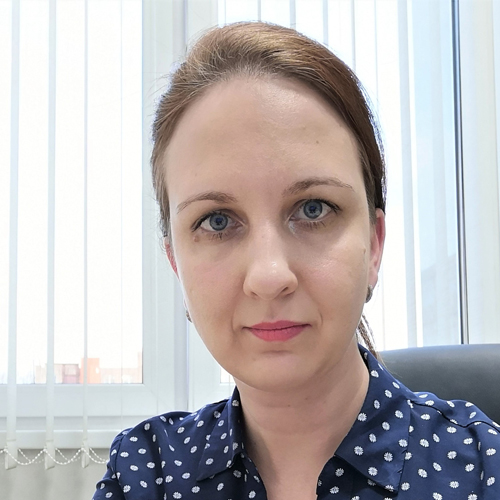
Ирина Хлупнова
руководитель ИТ-проектов компании «Цикл»В результате мы смогли улучшить управляемость и запасами, и производством в целом, повысить точность и эффективность как планирования производства, так и учёта продукции, материалов и полуфабрикатов.
Использовать систему «1С:ERP Управление предприятием 2» для регламентированного учета на предприятии пока не планируют. В ближайших планах развитие финансового планирования и бюджетирования. Ещё одна задача — перейти на версию «1С:ERP Управление предприятием 2.4», пока работа идёт на версии «1С:ERP Управление предприятием 2.1», на которой сделан проект.
Дальние перспективы — автоматизировать на системы «1С:ERP Управление предприятием 2» регламентированный учет. Тогда можно будет получать из этой системы бухгалтерский баланс, чтобы связать бухгалтерию с управленческим учетом в режиме онлайн. Также есть планы интеграции «1С:ERP Управление предприятием 2» с системой управления продажами на базе «1С-Битрикс24».