В компании «Микрон» разработали и внедрили модель управления производством, схему формирования производственной отчетности для управленческого и регламентированного учета, а также систему синхронизации справочников номенклатуры, общих для разных информационных систем предприятия. Сложность проекта обусловлена рядом отраслевых и индивидуальных особенностей организации процесса производства на предприятии. Первые измерения динамики нефинансовых количественных показателей позволили оценить результаты проекта как положительные. В частности, для критически важных позиций номенклатуры готовой продукции время непродуктивного ожидания очередных технологических операций сократилось от 0,5 до 4 раз. Продолжительность производственного цикла сократилась примерно на 5–7%. Простои из-за отсутствия необходимых материалов или полуфабрикатов сократились примерно на 15%.
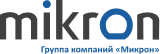
«Микрон» – крупнейший производитель и экспортер микроэлектроники в России, центр экспертизы и технологический лидер российской полупроводниковой отрасли. Микрон производит более 700 типономиналов продукции, включая интегральные схемы для защищенных носителей данных, идентификационных, платежных и транспортных документов, управления питанием и RFID-маркировки для различных отраслей цифровой экономики. «Микрон» входит в компанию «Элемент», объединившую микроэлектронные предприятия госкорпорации «Ростех» и АФК «Система». В компании работает более 1500 сотрудников.
Цель проекта: разработать модель системы управления производством.
Задачи проекта:
- Интегрировать модель в общий контур системы управления предприятием, включающий также управление продажами, обеспечением, разработками, персоналом и финансами.
- Использовать справочно-нормативную информацию, синхронизированную для управления всеми функциональными блоками предприятия, общей для управленческого и регламентированного учета.
- Решить ряд проблем управления производством, перечень которых консультантам предложено выявить самостоятельно в процессе диагностики и согласовать с заказчиком.
Компании потребовалось разработать модель системы управления, так как в производственном подразделении возникали трудности сквозного управления и формирования отчетности. В результате на предприятии происходили срывы графиков производства и исполнения заказов покупателей, возникали избыточные производственные запасы, замедлялось производство опытных образцов продукции, срывались сроки формирования управленческой и регламентированной отчетности, в отчетности периодически возникали ошибки, вызванные недостаточной достоверностью данных производственного подразделения.
Для автоматизации деятельности компания использует следующие программные подукты:
- 1С:Бухгалтерия;
- 1С:Зарплата и управление персоналом;
- 1С:ERP Управление предприятем;
- внутрицеховые mes-системы, управляющие производством на внутрицеховом уровне и регулирующими технологические режимы операций рабочих центров.
С использованием разработанной модели предполагается автоматизировать около 500 рабочих мест.
Виды консалтинговых работ на проекте:
- Моделирование и совершенствование бизнес-процессов.
- Диагностика существующих проблем в организации системы управления компанией и разработка рекомендаций для их устранения.
- Постановка управленческого учета и отчетности.
- Построение системы планирования и управления производством товаров, выполнения работ, оказания услуг.
- Разработка и внедрение системы управления ИТ-сервисами.
При выработке решений, предложенных клиенту, учитывались следующие методики, заложенные в систему «1С:ERP Управление предприятием».
- При создании структурной модели этапы производства выделены с учктом возможностей механизмов ресурсных спецификаций и маршрутных карт.
- Процессная модель управления производством на межцеховом и внутрицеховом уровне разработана в соответствии с возможностями функционала запуска и контроля этапов производства, настройки обмена данными с цеховыми mes-системами. Цеховые mes-системы автоматизируют внутрицеховое управление и задают технологические режимы обработки.
- Схема формирования производственной отчетности разработана в соответствии с порядком формирования себестоимости, заложенным в «1С:ERP Управление предприятием». Предусматривает выделение прямых номенклатурных, прямых постатейных и общецеховых косвенных производственных затрат.
- Схема работы и синхронизации справочников номенклатуры разработана с учетом возможностей справочника номенклатуры «1С:ERP Управление предприятием» и настроек ролей пользователей, предусматривает использование функционала дополнительных характеристик и настройки схем обеспечения материалами и полуфабрикатами.
- Решение выявленных проблем управления производством реализовано с учетом возможностей функционала планирования и контроля по этапам производства, оптимизации производственной программы по выбранному сочетанию критериев минимизации себестоимости и минимизации сроков производства:
-
- смешанная система планирования и управления запуском производства предусматривает доработку стандартного функционала с учетом возможностей планирования на основании плана продаж и на основании потребности;
- схема двойного учета полуфабрикатов в кристаллах и в пластинах на одном из этапов производства подразумевает доработку стандартного функционала с использованием ресурсных спецификаций, маршрутных карт, документа «Состав выпуска» и присвоения серийных номеров;
- система планирования производства, подразумевающая возможность размещения на одной пластине различных кристаллов, использует функционал ресурсных спецификаций;
- система планирования производства с учетом объединения на некоторых этапах и операциях в одну партию различных полуфабрикатов предполагает специальную доработку стандартного функционала с использованием механизмов ресурсных спецификаций, маршрутных карт, этапов производства и рабочих центров;
- схема сквозного планирования и контроля производства, учитывающая индивидуальные значения дополнительных характеристик готовой продукции в заказах клиентов, использует функционал обособленного обеспечения заказов по назначению;
- система серийной нумерации использует возможности функционалов серийных номеров, маркировки полуфабрикатов и дополнительных характеристик продукции;
- для построения раздельного учета использован функционал направлений деятельности и обособленного обеспечения заказов по назначению.
На прилагаемом рисунке отражены взаимосвязи системы производства с другими системами предприятия, значимые для описываемого проекта.
Сокращения:
- ЦПОП — центр планирования и отчетности производства;
- ПДО — планово-диспетчерский отдел.
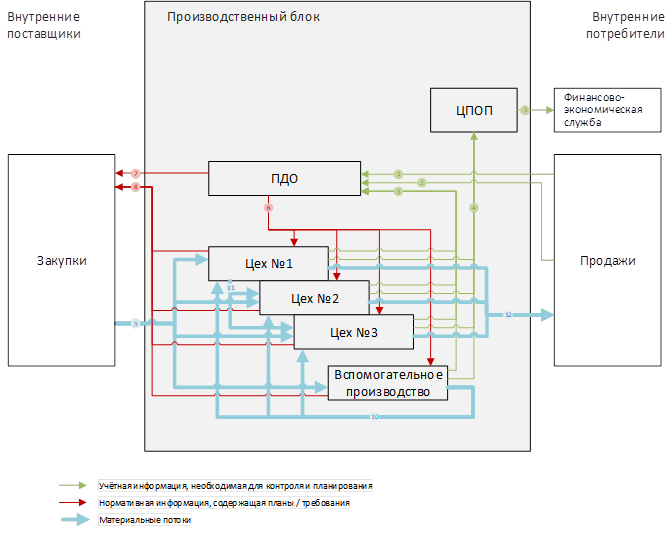
Связь системы производства с другими системами предприятия
Проведена диагностика системы управления производством. Выявлены ключевые проблемы, вызывающие сложности при планировании и контроле производства, приводящие к срыву графиков производства и поставок покупателям, затрудняющие ведение управленческого и регламентированного учета, приводящие к срыву сроков формирования отчетности, а именно:
- рассинхронизация справочников номенклатуры информационных систем, отвечающих за автоматизацию различных функциональных блоков предприятия, и справочников информационных систем внутрицехового и межцехового управления производством.
- отсутствие единого сквозного контура формирования управленческой и регламентированной отчетности.
- ряд особенностей процесса производства, не учитываемых системой операционного управления производством, приводящих к ошибкам в планировании и контроле, срыву графиков производства и сроков исполнения заказов покупателей.
- использование различных способов планирования производства для разных позиций номенклатуры готовой продукции:
- для продукции со стабильным спросом — на основании норматива неснижаемых запасов готовой продукции,
- для продукции с нестабильным спросом — на основании подтвержднных заказов клиентов;
- совместная передача годных и негодных полуфабрикатов с этапа производства выращивания кристаллов на этап производства отделения кристаллов от общей пластины и изъятия бракованных кристаллов. Данная особенность обусловлена технологическими условиями, при которых контроль качества возможен, пока кристаллы находятся на одной пластине.
- на одной пластине могут выращиваться как кристаллы, относящиеся к одной позиции номенклатуры, так и к разным позициям номенклатуры. Система управления производством Заказчика была настроена на условие, при котором на одной пластине могли выращиваться только кристаллы, относящиеся к одной номенклатурной позиции.
- на одной из дорогостоящих операций этапа измерения и отбраковки продукции в целях снижения затрат объединяются партии разных изделий с одинаковым режимом выполнения технологических операций. Система управления производством не предусматривала необходимость подобного способа формирования партий, в силу чего партии формировались ситуативно работниками рабочего центра и период ожидания обработки полуфабрикатов оказывался неоправданно долгим и неконтролируемым;
- на ряд позиций номенклатуры готовой продукции заказы разных клиентов предусматривают необходимость поставки изделий с разными характеристиками:
- толщина подложки, на которой располагаются кристаллы в готовой продукции,
- типоразмер корпуса продукции.
- система управления производством не учитывала необходимость планирования и контроля производства заказов с дополнительными характеристиками готовой продукции. В результате при производстве и распределении продукции возникала путаница, приводящая к срыву сроков производства и исполнения заказов;
- при сквозном планировании и учете производства на межцеховом уровне в разных производственных подразделениях использовались разные серийные номера и дополнительные характеристики продукции. В результате возникали ошибки в отчётности, контроле и планировании операций;
- выполнение части заказов клиентов, выполняемых в рамках гособоронзаказа, должно планироваться и учитываться обособленно. Система учета не предусматривала такую возможность. В результате приходилось прибегать к дополнительным операциям, не предусмотренным системой автоматизации, увеличивавшим трудоемкость и сроки формирования управленческой и регламентированной отчетности.
На основе проведенной диагностики разработана новая модель системы операционного управления производством, позволяющая интегрировать процесс производства в общий контур управления предприятием, своевременно формировать управленческую и регламентированную отчетность в рамках принятой учетной политики. Предложенная модель устранила выявленные на этапе диагностики проблемы.
- Разработана структурная модель процесса производства, основанная на выделении одиннадцати этапов производства, соответствующих технологическим переделам продукции.
- Разработана процессная модель операционного управления производством на межцеховом и внутрицеховом уровне.
- Разработана единая схема формирования производственной отчётности для нужд управленческого и регламентированного учета.
- Предложена схема работы со справочниками номенклатуры, обеспечивающая корректный ввод данных и синхронизацию во всех всех информационных системах.
- Предложены решения диагностированных проблем системы управления производством:
- смешанная схема планирования производства, предусматривающая:
- планирование производства на основе планов продаж и ожидаемого состояния запасов на плановый период для готовой продукции постоянного спроса
- планирование производства на основе подтверждённых заказов клиентов для готовой продукции непостоянного спроса,
- схема двойного учета полуфабрикатов кристаллах и пластинах на этапе выращивания кристаллов, предшествующего этапу отделения кристаллов от пластины.
- созможность планирования и учёта производства на одной пластине разных видов кристаллов, представляющих собой различные позиции номенклатуры полуфабрикатов, с учётом технологических ограничений.
- схему планирования и контроля отдельных производственных операций с объединением в одну партию обработки различных полуфабрикатов, относящихся к различной готовой продукции, с учётом технологических ограничений.
- схему сквозного планирования и контроля производства готовой продукции партиями с учётом дополнительных характеристик, заявленных в заказе покупателей.
- сквозную систему серийных номеров и дополнительных характеристик продукции для всех этапов производства, синхронизированную с другими функциональными блоками предприятия.
- систему обособленного планирования и контроля производства для государственных оборонных заказов.
Все перечисленные решения разработаны с учетом требований, адаптированы для автоматизации и смоделированы на функционале «1С:ERP Управляем предприятием». Предложенная модель операционного управления производством реализована в уже имеющейся на предприятии системе «1С:ERP Управляем предприятием».
В результате проекта предприятие получило следующие возможности:
- Формирование достоверной и оперативной отчетности производства для решения задач управленческого и регламентированного учета.
- Повышение эффективности системы планирования и контроля производства за счет оптимизации процессов управления, повышения достоверности и оперативности исходных данных.
- Снижение производственных издержек.
- Сокращение длительности производственного цикла.
- Сокращение продолжительности исполнения заказов покупателей и снижение количества срывов сроков исполнения заказов.
- Сокращение производственных запасов.
- Повышение качества обеспечения производства за счёт повышения качества производственного планирования.
Первые измерения динамики нефинансовых количественных показателей позволили оценить результаты проекта как положительные. В частности, для критически важных позиций номенклатуры готовой продукции время непродуктивного ожидания очередных технологических операций сократилось от 0,5 до 4 раз. Продолжительность производственного цикла в целом уже по результатам первых замеров в среднем для всего ассортимента сократилась примерно на 5–7%. Простои по причине отсутствия необходимых материалов или полуфабрикатов сократились примерно на 15%.