Компания Райтек внедрила на двух производственных площадках CERSANIT («Фряновский Керамический завод» и «Кучинский Керамический завод») информационную систему на базе «1С:ERP Управление предприятием». Автоматизировано 150 рабочих мест. Итог проекта автоматизации – создание единого интегрированного информационного пространства с глубокой цифровизацией производственного уровня.
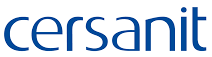
Cersanit специализируется на производстве сантехники и керамической плитки. Под брендом Cersanit в РФ работают три завода: два завода по производству керамической плитки и керамогранита в Подмосковье и завод по производству санитарной керамики в Самарской области.
Основная цель проекта автоматизации: создать единое интегрированное информационное пространство с глубокой цифровизацией производственного уровня.
Для достижения поставленной цели требовалось изучить имеющийся функционал «1С:Управление производственным предприятием», переработать и адаптировать его под «1С:ERP Управление предприятием», перенести данные, при этом не остановить работу сотрудников, которые уже работали в базе 1С:ERP, и решить следующие задачи:
- Перенести справочники в уже работающую 1С:ERP.
- Внедрить единые бизнес-процессы для всех компаний холдинга.
- Перевести площадки в единую систему с сохранением функциональности.
- Получить консолидированную управленческую информацию в единой учетной системе.
На момент старта проекта на предприятии была развернута следующая ИТ-архитектура.
На двух производственных предприятиях заказчика («Фряновский Керамический завод» и «Кучинский Керамический завод») использовалось решение «1С:Управление производственным предприятием» (УПП), которое было сильно кастомизировано под собственные задачи. Были разработаны десятки собственных документов и отчетов, такие как:
- Отчет мастера смены.
- Загрузка отчетных карт
- Форма заказа мастик.
- Процесс декорирования артикула.
- Формирование отчета производства за смену.
- Использование спецификаций в производстве.
- Выгрузка карт загрузки.
- Формирование отчета производства за смену (мокрый вес).
- Распределение сырья в пределах норм допустимых потерь.
- Печать спецификаций.
- Контроль списания сырья по нормативам.
- Печать спецификаций (с компонентами).
- Отчет для контроллинга (Working Capital).
- Формирование дерева спецификаций.
Сложности и недостатки текущей информационной системы:
- Устаревшая ИТ-архитектура. «1С:Управление производственным предприятием» было невозможно обновить. Отсутствовали возможности для развития системы. Имеющийся функционал отставал от требований бизнеса.
- Сложности в документообороте между организациями группы компаний, т.к. они имели различные процессы.
- Огромные трудозатраты по подготовке отчетных форм, а также по проверке внесенных данных. Отчетность не была оперативной.
- Низкая прозрачность производственных процессов, трудоемкий расчет цеховых KPI.
Единая информационная система компании построена на базе «1С:ERP. Управление предприятием 2». Автоматизированы следующие ключевые блоки:
- закупки;
- ремонты;
- производство;
- складская логистика;
- продажи;
- бухгалтерский и налоговый учет;
- казначейство;
- бюджетирование.
Схема архитектуры
Пояснения к схеме:
Comarch EDI — платформа для электронного обмена документами (работает на основе технологии EDI − Electronic Data Interchange).
EDI EdiSoft — облачное решение для работы с поставками.
Avalon — система для выгрузки отчетности по МСФО.
Penta WMS — система складского учета.
Cons Org — cправочная правовая система.
Портал — внутрикорпоративный портал.
Cersanit Trade — ООО «Церсанит Трейд».
Cersanit FKZ/KKZ — «Фряновский Керамический завод» / «Кучинский Керамический завод».
Cersanit SKZ — АО «Сызранская керамика».
Перед командой стояла сложная задача не просто перевести предприятие в новую конфигурацию, а за полгода перевести одновременно два завода в базу, в которой уже 1,5 года работает другое предприятие. При этом никак не ухудшить процессы, которые годами формировались в исторических системах, и обеспечить тем же набором инструментов, что и ранее. При этом ни одно предприятие не должно было останавливаться и сроки предоставления управленческой отчетности надо было сохранить на прежнем уровне: 5 числа месяца, следующего за отчетным.
Решить эту задачу позволило следование основной концепции проекта, которая заключается в следующем:
- Минимизация объема доработок без ущерба функциональности:
-
- минимизации сроков и затрат на реализацию проекта по автоматизации учета;
- минимизации сложности и затрат на дальнейшую поддержку (в т.ч. обновлений) подсистемы.
- Внедрение проходило по очередям:
- 1-я очередь: внедрение критически важного функционала;
- 2-я и 3-я очереди: развитие АС.
- Объем технической документации — в рамках разумного.
Сократились трудозатраты в подразделениях
Итогом проекта стали:
- Создание единой интегрированной среды планирования на предприятии.
- Отказ от устаревшей ИТ-архитектуры и от использования Excel.
- Повышение скорости формирования и достоверности управленческой отчетности.
- Создание информационной среды для эффективного взаимодействия всех организаций, определенных в проекте, и их подразделений в рамках сквозных бизнес-процессов.
Одним из показателей экономического эффекта является сокращение трудозатрат в подразделениях, показатель составил 10%.
Реализованная концепция цифровизации на предприятии создала возможность тиражирования данного решения на остальные производственные площадки группы компаний CERSANIT.