Компания «Восток-Сервис» перешла на отечественную систему «1С:WMS Логистика. Управление складом». Автоматизирован учет продукции в разрезе дат изготовления, сроков годности и производителей. Реализован механизм прослеживаемости продукции, подлежащей обязательной маркировке, а также возможность обработки продукции на всех этапах с учетом нахождения продукции в контейнерах и мастер-контейнерах. Оптимизирован партионный учет товаров. Повысилась эффективность хранения, уменьшилось количество неликвидных остатков и запасов, поставленных под конкретных контрагентов, что позволило увеличить количество свободных мест хранения товара. Внедрение открыло новые возможности для роботизации складского комплекса.

Группа компаний «Восток-Сервис» — крупнейший в России разработчик, производитель и поставщик спецодежды, спецобуви и средств индивидуальной защиты (СИЗ). В 56 регионах России, Беларуси, Казахстане, Азербайджане работают более 120 филиалов компании. Розничная сеть представлена 280 фирменными магазинами, расположенными в 170 городах России и стран СНГ.
Цели проекта:
- Перейти на отечественное ПО.
- Повысить эффективность использования складских площадей (в т.ч. зон штучного отбора).
- Повысить качество работы с товаром в разрезе даты производства и производителя.
- Усилить контроль выполнения операций приемки, хранения, комплектации и отгрузки продукции со склада с учетом меняющихся требований клиентов к формированию грузовых мест и остаточным срокам годности.
Задачи проекта:
- Ускорить комплектацию заказов за счет автоматизации основных бизнес-процессов, в том числе за счет перехода от схемы пополнения зоны штучного отбора продукции (мезонина) «Под потребность» к схеме пополнения под «Красные линии» (min/max).
- Обеспечить прослеживаемость товара, подлежащего обязательной маркировке.
- Реализовать возможность гибкой настройки различных сценариев отбора и размещения продукции.
- Рассчитывать:
- производительность сотрудников склада.;
- KPI по количественным и временным показателям работы сотрудников.
- Обеспечить возможность кастомизации расчета показателей.
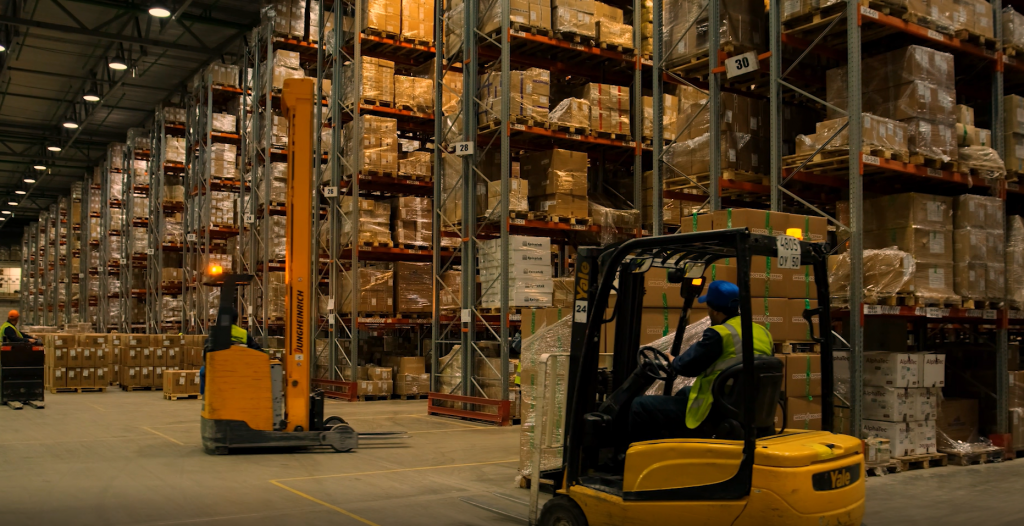
Основными предпосылками для внедрения новой системы автоматизации склада послужили:
- Необходимость перехода на отечественное ПО.
- Отсутствие механизма отслеживания положения продукции, подлежащей обязательной маркировке, в режиме реального времени.
- Отсутствие механизмов гибкой настройки алгоритмов размещения, отбора и пополнения продукции, а также выбора линий отгрузки.
- Отсутствие правил совместимости товаров при сборке заказов.
- Отсутствие инструмента оценки эффективности работы складских сотрудников.
- Возможность использования RFID-туннелей и интеграции оборудования с новой системой.
- Необходимость роботизации складского комплекса в перспективе ближайших 2-3 лет.
WMS-система компании построена на базе ршения «1С:WMS Логистика. Управление складом». Автоматизированы:
- Приемка.
- Отгрузка.
- Внутренние операции.
- Управление ресурсами.
- Интеграция с учетной системой.
- Интеграция с периферийным оборудованием.
- Интеграция с различными сервисами компании.
- Цифровая маркировка товара.
- Анализ показателей эффективности работы склада и складских сотрудников.
Масштаб проекта
Под управлением 1С:WMS находится:
- 38 100 паллетомест;
- 6 000 кв.м. зоны штучного отбора (мезонин), зоны комплектации;
- 2 000 кв.м зон хранения негабаритной продукции;
- 9 000 кв.м. зон хранения низкооборачиваемых товаров.
Количество автоматизированных рабочих мест:
- более 140 рабочих мест;
- в том числе на ТСД более 60.
- Руководство поставило задачу перейти на новую WMS без остановки склада, в связи с этим была определена технология внедрения «Мягкий запуск» без остановки склада. Переходили поэтапно, постеллажно, зонально. Начинали переход с одного стеллажа. Это означает остановку стеллажа всего на час-два. Выведение данных из прежней системы, загрузка в 1С:WMS. Первоначально переводили не более одного стеллажа в день, к концу внедрения зоны коробочного хранения скорость выросла до 5 стеллажей в день, при их общем количестве 84 ряда. Приблизительно по такой же схеме внедрялся мезонин и другие типы зон хранения на СК «Раменское».
- Реализован уникальный механизм расчета количества продукции, необходимого для пополнения в зоны мезонина «под красные линии» (min/max). Также данный механизм позволяет «вытеснять» низкооборачиваемую продукцию из зон мезонина в специально предназначенные для такой продукции зоны.
- Разработана интеграция с RFID оборудованием (RFID туннели для приемки и отбора продукции, подлежащей обязательной маркировке).
- Разработан новый механизм, позволяющий по заданным условиям и алгоритмам планировать линии отгрузки (ячейки хранения продукции после отбора до отгрузки в транспортное средство).
- Разработан механизм компрессии (уплотнения, дефрагментации) продукции под разные сценарии (один ко многим, многие к одному) и с учетом хранения продукции в мастер-контейнерах.
- Разработаны рабочие места приемки и отбора для зон хранения негабаритной и низкооборачиваемой продукции.
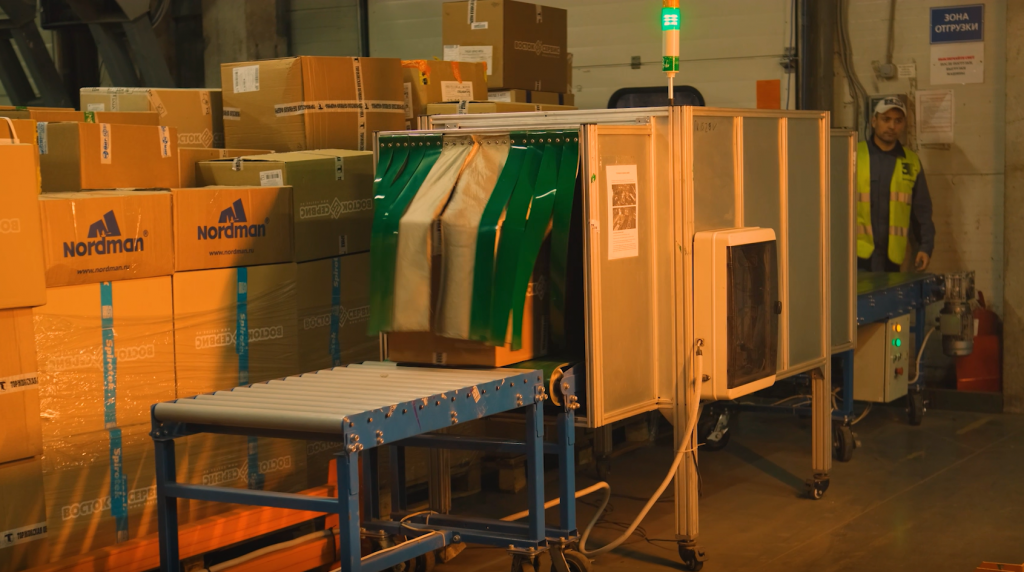
Снижение объемов материальных запасов
Рост оборачиваемости складских запасов
Ключевые эффекты от внедрения:
- За счет более оптимального механизма пополнения зон мезонина удалось снизить их заполненность, что позволило увеличить объем отгрузки и снизить количества ошибок при отборе.
- В процессе отбора продукции соблюдаются такие ключевые показатели, как: FPFO, кратность отбора, наличие актуального сертификата на продукцию, необходимость отгрузок в миниупаковках, правила формирования грузовых мест и многое другое.
- За счет наличия гибких механизмов настройки условий и алгоритмов планирования размещения, отбора, подпитки и линий отгрузки, сократилось время реакции на изменяющиеся требования как от покупателей, так и от подразделений компании.
- Оптимизирован партионный учет товаров. Повышена эффективность хранения, уменьшено количество неликвидных остатков и запасов, поставленных под конкретных контрагентов, что позволило увеличить количество свободных мест хранения товара.
- Внедрен механизм оценки эффективности работы складских сотрудников.
- У ОТК появился инструмент для разделения зон ответственности, кто за какую категорию товара отвечает.
- За счет нового механизма распределения клиентских заказов по линиям отгрузки появилась возможность распределять грузопотоки при комплектации согласно внутренним потребностям складского комплекса и общим потребностям разных направлений логистики — автоперевозки, ЖД, авиа и другие.
- Внедрение 1С:WMS открыло новые возможности для компании по достижению бизнес-цели компании, а именно роботизация складского комплекса.
Достигнуты следующие результаты:
- Реализована интеграция и обмен данными с корпоративными информационными системами (зарубежной ERP-системой, 1С:MDM и др.). При разработке реализованы интеграционные потоки с использованием шины данных и http-сервисов.
- Реализован учет продукции в разрезе дат изготовления, сроков годности и производителей.
- Реализован механизм прослеживаемости продукции, подлежащей обязательной маркировке.
- Реализована возможность обработки продукции на всех этапах (приемка, размещение, отбор, подпитка, компрессия и отгрузка) с учетом нахождения продукции в контейнерах и мастер-контейнерах.
- Настроены расширенные сценарии планирования задач на размещение, отбор, подпитку и компрессию (дефрагментацию).
- Разработан механизм, позволяющий использовать расширенные сценарии планирования линий отгрузки.
- Проработан механизм работы с товаром, снабженным RFID-метками.
- Разработаны рабочие места по работе с использованием RFID-туннелей.
- Разработаны рабочие места приемки и отбора на складах с отсутствием технической возможности использования ТСД.
- Разработано рабочее место диспетчера склада, с возможностью оперативного изменения приоритета и исполнителей задач.
- Внедрены правила совместимости товаров при сборке заказов (например, нельзя в одном коробе смешивать товары несовместимых категорий).
- Подбор короба для сборки заказов, исходя из ВГХ собираемых товаров.
- Произведена оцифровка складов, то есть теперь есть возможность посчитать как количество подходов к ячейке, так и количество скомплектованных коробов, выполненных операций.
- Проведена адаптация к новой системе более чем 200 сотрудников.
Экономический эффект от внедрения:
- снижение объемов материальных запасов — 20%;
- рост оборачиваемости складских запасов — 18%;
- сокращение сроков исполнения заказов / оказания услуг — 10%;
- сокращение трудозатрат в различных подразделениях — 20%;
- ускорение обработки заказов — 17%.
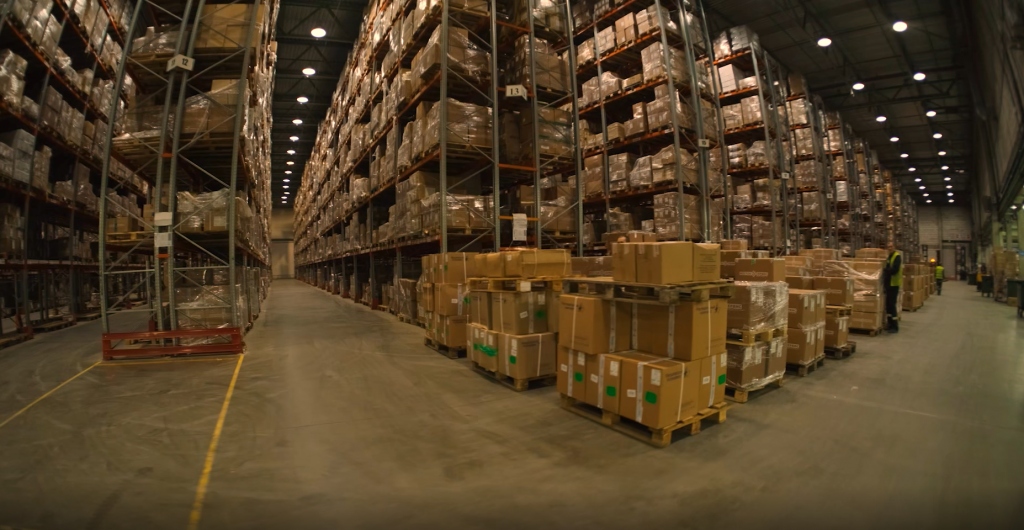