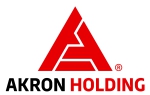
Гайский завод по обработке цветных металлов — один из ключевых производителей плоского проката (медного, латунного, медно-никелевого и никелевого) на рынках России и Ближнего зарубежья. Входит в состав группы компаний AKRON HOLDING.
Цель проекта: обеспечить контроль и сохранность материально-производственных запасов, готовой продукции.
Задачи проекта:
- Создать методологию управления плавильным и прокатным производством для масштабирования на все профильные предприятия холдинга.
- Определить себестоимость производства и баланс металла, сократить непродуктивные потери.
- Обеспечить выполнение стандартов финансовой отчетности (РСБУ, МСФО) для предоставления информации в управляющую компанию, работы с внешними финансовыми организациями, банками, партнерами.
- Оптимизировать трудозатраты и автоматизировать рабочие места производственников.
- Сократить время подготовки отчетности и разработать автоматические светофорные показатели.
До внедрения «1С:ERP» на заводе использовалось решение «1С:Управление производственным предприятием», в котором не были реализованы детальный учет производственных операций, бизнес-процессы приемки и обработки лома, плавильного и прокатного производства, приемо-сдаточных испытаний.
Для компенсации этого недостатка старой информационной системы применялись различные специализированные программы учета выпуска проката и плавильного производства. Однако, отсутствовала интеграция как между «1С» и специализированными решениями, так и между самими специализированными программами. Не была реализована автоматизированная система диспетчеризации производства.
Фактически проектным командам исполнителя и заказчика пришлось проектировать некоторые бизнес-процессы «с нуля», обосновывать их экономическую целесообразность и защищать перед собственниками бизнеса новую модель IT-ландшафта предприятия.
Было принято решение о переходе на актуальную версию ERP-системы от «1С» — «1С:ERP Управление предприятием 2». Для выполнения проекта руководство холдинга выделило собственную IT-команду и обратилось за помощью в «1С-Рарус».
Система оперативного и регламентированного учета построена на базе «1С:ERP Управление предприятием 2». Потребителями данных информационной системы выступает управляющая компания холдинга, все предприятия холдинга, задействованные в технологической и логистической цепочке производства гайского завода и отчасти покупатели продукции завода. На запуск автоматизированной системы в промышленную эксплуатацию потребовалось 6 месяцев.
Автоматизированы следующие функции:
- Закупки (снабжение) и управление отношениями с поставщиками:
- оформление заказов поставщикам,
- планирование закупок.
- Производство, услуги:
- объемно-календарное планирование производства;
- планирование потребности в материалах;
- расчет фактической себестоимости;
- управление данными о составе и структура изделия, рецептура;
- управление данными о технологии производства с учетом выпускаемой потребности (параметризуемые спецификации изделий);
- учет затрат на производство;
- учет производственных заказов.
- Продажи:
- планирование продаж в разрезе менеджеров/планов/видов скидок;
- оформление заказов клиентов — загрузка из внешней системы, ручное оформление;
- продажи интернет-магазина;
- управление видами скидок продаж;
- управление продажами в разрезе распределительных центров ритейлов.
- Склад и логистика:
- автоматизация ордерного склада;
- учет себестоимости по сериям;
- автоматизация обмена с внешней системой 3-PL оператора.
- Бухгалтерский учет.
Схема архитектуры
В рамках проекта процессы завода автоматизированы с учетом отраслевой специфики, причем некоторые бизнес-процессы спроектированы «с нуля».
Проектная команда создала методологию, которая сохраняет максимально типовой функционал «1С:ERP Управление предприятием» и учитывает особенности плавильного и прокатного производства. С нуля разработан расчет «Баланса металла», ключевой для контроля потерь на металлургическом предприятии — брака, сливов, скрапа и т.д.
Рост прибыли
Совместная проектная команда заказчика и исполнителя провела работу над автоматизацией процессов завода и адаптацией «1С:ERP» к отраслевой специфике:
- Определены объекты учета и контролируемые операции от регистрации заказа клиента до реализации готовой продукции. Появилась возможность управлять детализацией требуемых для производства ресурсов.
- Оптимизирована система финансовых и производственных отчетов, были удалены дублирующие и неиспользуемые отчеты.
- Автоматизированы рабочие места сотрудников, обеспечивающих контроль движения сырья от поступления до сдачи готовой продукции. Реализованы АРМ Плавильщика, АРМ Оператора рабочего центра, АРМ выполнения операций. АРМ позволяют:
- формировать сменные задания для полунепрерывного производства слитков.
- отражать загрузку шихтового материала в печь.
- отслеживать выполнение производственных операций.
- контролировать движение заготовки по этапам производства.
- проводить анализ причин остановки производственного процесса.
- идентифицировать заказ по сериям.
- управлять процессом лабораторных анализов, формировать наряды на испытания.
- Обеспечен контроль образования оборотных, возвратных, товарных отходов и безвозвратных потерь.
- Обеспечен расчет себестоимости по прямым затратам.
- Спроектирована и реализована система контрольных и управленческих отчетов, настроены оповещения о сверхнормативных отклонениях на каждом этапе производства.
- Обеспечен анализ «по контрольным точкам» в количественном и/или весовом выражении наличия ТМЦ на складах, материалов, переданных в производство, выпущенных производством полуфабрикатов, возвратных, оборотных отходов и безвозвратных потерь. Это позволяет эффективно управлять остатками сырья в НЗП, используя их для производства новых заказов. Результат достигается за счет:
- Использования автоматической подсистемы взвешивания для сбора данных о весе сырья, заготовки, готового изделия.
- Идентификации изделий штрихкодированием и присвоением паспортов изделия.
- Для определения брака по химическому составу был разработан уникальный функционал «Данные химического анализа», на основании которого формируется отчет по химическому составу за период.
В результате внедрения прибыль предприятия выросла на 12,6%, сократились трудозатраты, а производительность труда персонала выросла на 17%.