На четырех крупных предприятиях — «Нижнекамск шина», «Нижнекамский Завод Грузовых Шин» и «Нижнекамский Завод шин ЦМК», а также на «Нижнекамском Механическом Заводе», осуществляющем техническое обслуживание и ремонт оборудования — создана система управления ремонтами и обслуживанием оборудования. В информационной системе, построенной на базе «1С:Предприятие 8. ТОИР Управление ремонтами и обслуживанием оборудования», находится более 10 000 объектов ремонта. Благодаря системе руководители предприятия своевременно получают всю необходимую и корректную аналитическую информацию. В результате, ремонт производится более оперативно, время простоя техники сокращено почти на 1700 часов в год. Производственные издержки от простоев техники снижены на 30%. Оптимизирован процесс планирования ресурсов, складские запасы сокращены на 7%, это позволило сэкономить более 4 млн. рублей за год.
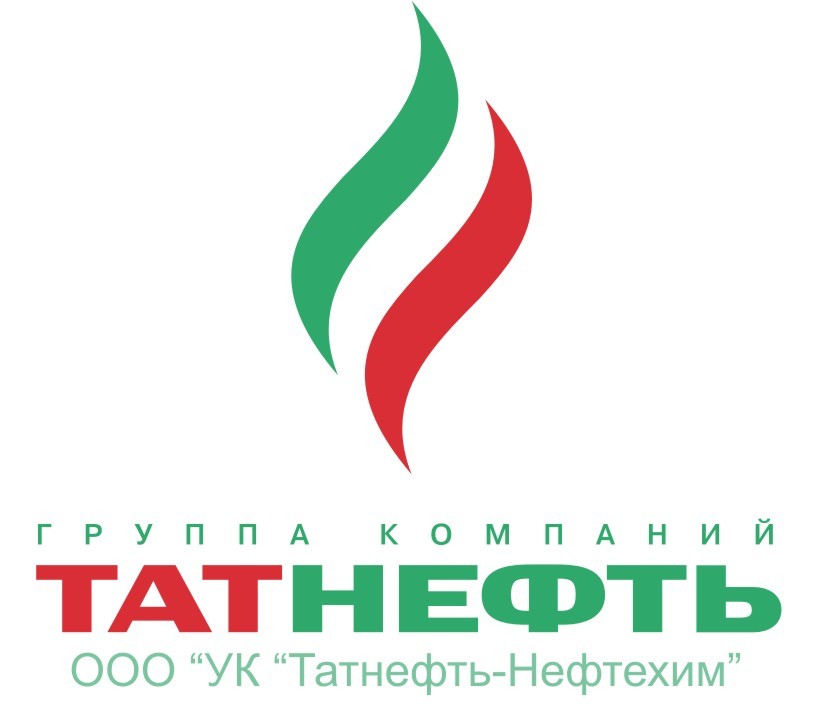
Управляющая компания «Татнефть-Нефтехим» — дочернее компания холдинга «Татнефть», создана в 2002 г. для управления нефтехимическим комплексом холдинга. В её составе объединены предприятия, тесно связанные с производством шин: «Управляющая компания „Татнефть-Нефтехим“», «Нижнекамскшина», «Нижнекамский завод грузовых шин», «Нижнекамский завод технического углерода», «Нижнекамский механический завод», «Ярполимермаш-Татнефть», «Торговый дом „Кама“», «Татнефть-Нефтехимснаб», «Научно-технический центр „Кама“», «Нижнекамский завод шин ЦМК», «Энергошинсервис».
Цели проекта:
- повышение эффективности эксплуатации оборудования и управления техническим обслуживанием и ремонтами;
- оптимизация управления персоналом;
- оптимизация складских запасов и закупок.
Для достижения поставленных целей требовалось решить следующие задачи:
- создание единой базы технологического оборудования;
- автоматизация ведения графиков планово-предупредительных ремонтов;
- уход от «ручного» планирования доходов по продаже и эксплуатации оборудования
- оптимизация затрат на содержание и ремонт технологического оборудования;
- сокращение времени согласования документов с финансовой службой завода и с клиентами;
- повышение производительности и эффективности работы в целом, снижение прямых и косвенных издержек.
Ранее задачи управления техническим обслуживанием и ремонтами на предприятии не были автоматизированы. Отсутствовала единая база технологического оборудования. Для учёта объектов ремонта, простоев, запасных частей и материалов, расчёта потребности в техническом персонале и оборудовании использовались, преимущественно, электронные таблицы. Составить детальный отчёт и проанализировать работу с их помощью достаточно сложно. Графики планово-предупредительных ремонтов составлялись вручную. Было сложно планировать обслуживание техники и закупку материалов. Много времени уходило на согласование документов с финансовой службой завода и с заказчиками.
Руководство управляющей компании приняло решение о создании информационной системы, которая позволила бы наладить точный учёт объектов ремонта, обеспечить бесперебойные поставки запчастей и комплектующих. Необходимо было улучшить качество планирования работ по обслуживанию техники, оптимизировать затраты на содержание и ремонт оборудования, ускорить согласование сопроводительных документов.
Для решения этих задач были выбраны программные продукты «1С:Предприятие 8. ТОИР Управление ремонтами и обслуживанием оборудования» и «1С:Управление промышленным предприятием 8», объединённые в единую систему.
Система интегрирована с системой учёта простоя оборудования, заявки на ремонт формируются из фактов фиксации простоя техники.
Система охватывает 100 автоматизированных рабочих мест для планировщиков, диспетчеров, начальников цехов и их заместителей по оборудованию, руководителей и мастеров ремонтных служб, главных специалистов заводов и управляющей компании, а также высшего руководства. Одновременно в ней работают около 30 пользователей. В сутки обрабатывается до 1200 заявок.
Система система управления ремонтами и обслуживанием оборудования внедрена на четырёх крупных предприятиях — «Нижнекамск шина», «Нижнекамский Завод Грузовых Шин» и «Нижнекамский Завод шин ЦМК», а также на «Нижнекамском Механическом Заводе», осуществляющем техническое обслуживание и ремонт оборудования.
В информационной системе находится более 10 000 объектов ремонта. Проект был выполнен в короткие сроки — всего за 6 месяцев.
Для упрощения ввода информации о ремонтах были разработан документ-заявка, который автоматически создает типовые документы по остановке оборудования, фиксации дефекта, создании заявки и оформления акта.
Оптимизирован процесс планирования ресурсов, складские запасы сокращены на 7%, это позволило сэкономить более 4 млн. рублей за год. Если ранее графики планово-предупредительных работ составлялись и корректировались вручную, занимая у сотрудника до 40 часов, то сейчас построение и согласование графиков происходит путём нажатия одной кнопки и вместе с дополнительными корректировками занимает максимум 4 часа в месяц. При формировании графика планово-предупредительных работ система автоматически рассчитывает потребность в запасных частях, материалах и инструментах. Поскольку все операции с запасами отслеживаются в режиме реального времени, всегда имеется актуальная информация о складских остатках, материалах и запасных частях, отпущенных на выполнение работ, и о фактическом расходе материалов. Опираясь на достоверную информацию, служба материально-технического обеспечения может вовремя скорректировать план работы, отправить соответствующие заявки на поставку, пополнить складские запасы и быстро обеспечить технический отдел необходимыми запчастями и материалами. Это позволяет экономить время и деньги. Автоматизация процесса планирования и сокращение уровня запасов позволили работать более эффективно, сократив затраты на содержание и ремонт оборудования более чем на 4 млн рублей в год.
Улучшен контроль процесса техобслуживания оборудования. Производственные издержки от простоев техники снижены на 30%. Составлять и проверять графики обслуживания и ремонта техники теперь стало гораздо удобнее. Теперь система автоматически собирает статистические данные об интенсивности эксплуатации, количеству поломок и ремонтных работ по каждому виду оборудования. Анализ данных помогает снижать простои оборудования и складские запасы, определять выгоду и целесообразность использования, обслуживания и ремонта используемой техники. Техническая документация находится в единой базе, что позволяет обеспечить оперативный доступ к информации. Сейчас на получение всех необходимых данных уходит не более 5 минут, а ранее это могло занимать до 8 часов. Сотрудники могут уделять больше времени контролю состояния, работоспособности и надёжности оборудования. Ремонт производится более оперативно, время простоя техники сокращено почти на 1700 часов в год.
Трудозатраты на согласование документов снижены на 15%. Экономический отдел получил удобный инструмент для расчёта и учёта средств, требующихся на техническое обслуживание и ремонт оборудования. Используя информацию о планируемых ТО и ремонтах, планово-экономический отдел распределяет бюджет более рационально, что позволяет увеличить эффективность расходов. В новой системе документы для бухгалтерии оформляются точно в срок, без ошибок и неточностей. Всё это экономит время и силы технических специалистов, затраты на согласование документов между службами ремонта завода и заказчиками снижены в среднем на 15%.