Машиностроительный холдинг «РМ-Терекс» построил единую систему управления производством и сбытом на своих заводах и в торговом доме. Для целей централизации учёта и планирования производства было выбрано решение «1С:ERP Управление предприятием 2». Проект запускался в два этапа. На первом этапе были автоматизированы процессы продаж, закупок, сервисного и гарантийного обслуживания, регламентированного бухгалтерского и налогового учёта в торговом доме «РМ-Терекс». На втором этапе были автоматизированы процессы оперативного производственного учёта и планирования производства на заводе «Тверской экскаватор». В 2018 году система тиражируется на остальные заводы группы. Создание системы позволило отказаться от разрозненных систем, повысилось качество и точность планирования производства на пилотном заводе, скорость обработки заказов увеличилась на 25%, удалось добиться сокращения запасов ТМЦ на 10% и до 5% — сокращения производственного цикла.

Компания «РМ-Терекс» — совместное предприятие российской корпорации «Русские машины» и многоотраслевого мирового производителя «Terex Corporation», входит в состав машиностроительной промышленной группы «Базовый Элемент». Объединяет крупные машиностроительные заводы России: «Тверской экскаватор», «Брянский арсенал», «Челябинские строительно-дорожные машины», «Заволжский завод гусеничных тягачей». Основные виды продукции: экскаваторы-погрузчики, колёсные и гусеничные экскаваторы, автогрейдеры, гусеничные снегоболотоходы. Численность сотрудников предприятия — более 2000 человек.
Ключевые бизнес-цели:
- обеспечить единое информационное пространство для торгового дома и производственных площадок;
- поднять качество сервиса;
- увеличить скорость обработки заказов;
- повысить управляемость остатками НЗП;
- снизить трудоёмкость процессов оперативного планирования производства;
- сократить остатки ТМЦ на складах;
- повысить скорость принятия решений при изменении внешних факторов.
Задачи проекта:
- автоматизировать процессы продаж в торговом доме;
- обеспечить эффективное взаимодействие заводов и торгового дома в рамках процессов планирования производства, отгрузки готовой техники, сервиса и гарантии;
- автоматизировать процессы сервисного и гарантийного обслуживания, включая взаимодействие с дилерами;
- разработать и внедрить единую модель управления производством и качеством продукции для всех заводов холдинга;
- автоматизировать процессы складкой логистики и управления запасами в торговом доме и yf складах заводов, включая ордерный ячеистый учёт;
- обеспечить консолидированный процесс закупочной деятельности по всем заводам.
Низкая управляемость остатками НЗП, трудоёмкий процесс оперативного планирования производства, завышенные остатки ТМЦ на складах — одной из причин возникновения этих проблем была далёкая от совершенства ИТ-архитектура на заводах и в торговом доме. Для управления производством на заводах холдинга использовались системы собственной разработки на базе FoxPro, которые были сложны в поддержке и не отвечали требованиям бизнеса. Отсутствовала полноценная система планирования производства, как следствие, невозможно было точно рассчитать производственную программу, а также выполнить быстрый пересчёт графика производства при изменении портфеля заказов. Торговый дом и заводы работали в отдельных системах (на базе «1С:Управление производственным предприятием», «1С:Управление торговлей» и FoxPro), поэтому необходимо было поддерживать большое количество интеграционных сервисов. Это приводило к периодическим сбоям при обменах, коллизиям в части нормативно-справочной информации, вызывало сложности для торгового дома по оперативному получению информации от производственных площадок.
Централизованная система управления производством и сбытом выполнена на базе тиражного решения «1С:ERP Управление предприятием 2».
Выполнять проект было решено поэтапно: в 2017 году автоматизировать процессы торгового дома и завода «Тверской экскаватор», а в 2018 году тиражировать систему на заводы «Брянский арсенал», «Челябинские строительно-дорожные машины», «Заволжский завод гусеничных тягачей». На первом этапе были автоматизированы процессы сервисного обслуживания и гарантийного обслуживания в торговом доме, оперативный производственных учёт и планирование производства завода «Тверской экскаватор».
НСИ, необходимая для работы «1С:ERP Управление предприятием 2», загружается из внешней PDM-системы. В рамках проекта реализован полноценный обмен с загрузкой всех необходимых данных для справочника «Ресурсные спецификации».
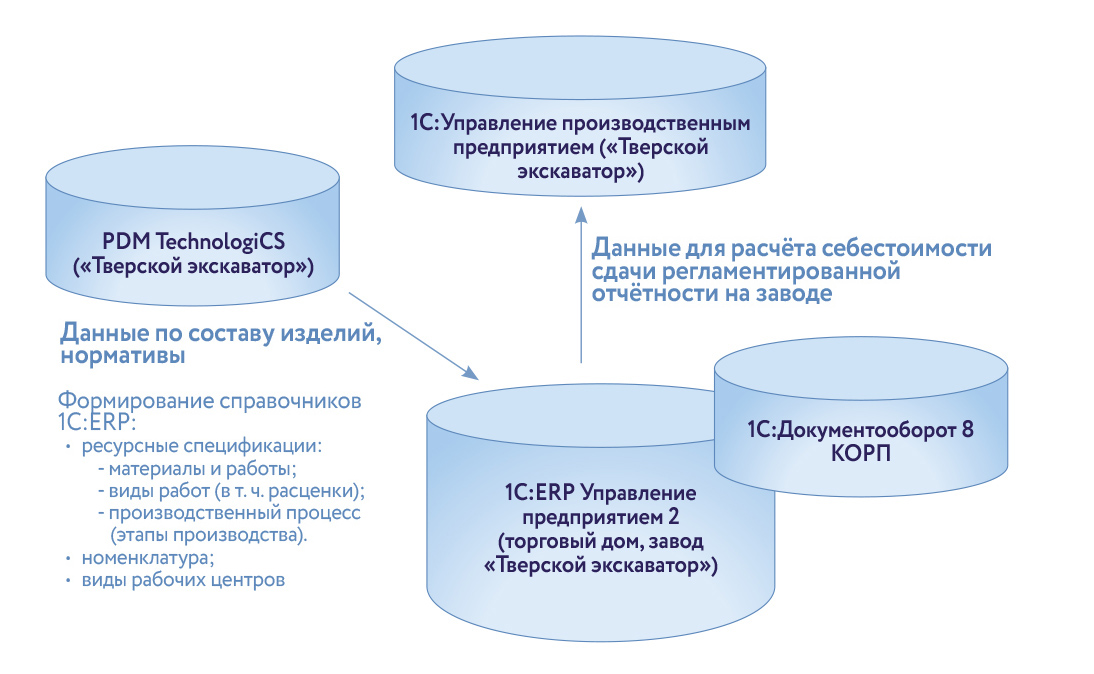
В блоке «Продажи» автоматизировано управление заказами клиентов, в том числе комплектация и конфигурирование заказа с учётом различных опций по предлагаемой технике. Для этих целей были проведены доработки типового функционала в части документа «Заказ клиента», а также добавлены дополнительные справочники. Блок «Продажи» интегрирован с блоком сервисного и гарантийного обслуживания, которые реализованы как дополнительные системы. Для взаимодействия с дилерами используется функционал подключения внешних пользователей через веб-доступ. Причём отгрузки торгового дома увязаны со сроками производства на заводе.
Блок «Закупки» — типовой с минимальными доработками, реализована связь с производством комплектующих на заводе. Непосредственно на заводе блок «Закупки» также внедрён без доработок: заказы поставщикам формируются на основании планов закупки, которые в свою очередь формируются на основании трёхмесячных планов производства.
В блоке «Управление и планирование производства» реализована методика подготовки планов производства. Номенклатура распределяется по переделам:
- заготовительный — детали, технологический процесс которых начинается в заготовительном цехе;
- сборка — детали, технологический процесс которых начинается в сборочном цехе;
- механообработка — все остальные детали.
Проведена настройка справочника «Ресурсные спецификации». Справочник настроен с учётом специфики предприятия: детали заготовительного и механо-сварочного производства производятся без привязки к заказу — на склады готовых деталей, а узлы и сборочные единицы, которые поступают на сборочный конвейер — настроены как «Производить по спецификации». Это позволяет для сборки по одному заказу производства видеть дерево этапов разных подсборок/узлов, которые выполняются так же в сборочном цехе.
Планы производства формируются на три месяца и на месяц, разбиваются по направлениям производства для снижения количества строк в одном документе. План по выпуску готовой продуктции на следующий месяц (по дням) создаётся вручную начальником производственно-диспетчерского отдела. Он является планом отгрузок и на основании этого плана создаются заказы на производство. По ним создаются этапы. Каждый заказ на производство содержит дерево этапов, которые выполняются в сборочном цехе. При необходимости можно заменить выпуск одной машины на другую, т. е. можно удалить одно дерево этапов и создать другое, при этом детали и узлы будут использоваться из прежних планов. Планы на механообработку и заготовительное производство создаются на основании разузлованных трёхмесячных планов. По ним создаются заказы на производство: один заказ на производство на одну номенклатуру, без деревьев подчинённых этапов.
Также была разработана подсистема для оперативного планирования производства, которая решает задачи перепланирования/пересвязывания деталей переделов заготовительного и механообработки в случае, когда это необходимо: определяет сроки выпуска продукции, количество деталей, которые надо запустить для новых заказов на производство на машину, количество деталей, которые по плану производятся, но теперь остаются невостребованными. Подсистема позволяет принимать решение о корректировке заказа на производство, оценить ситуацию по обеспеченности производства на текущее расписание производства.
Для учёта факта выполнения производстенных заданий была разработана отдельная подсистема, которая позволила отражать выработку сотрудников, сдаточные накладные и прочее, с учётом специфики каждого отдельного цеха. В части подсистемы контроля качества обеспечена прослеживаемость ключевых узлов и компонентов техники: прослеживаемость реализована с использованием механизма серийного учёта. Отдельно стоит отметить разработку подсистемы для учёта раскройных листов. Подсистема была разработна «с нуля» и увязана с основной подсистемой управления производством.
Автоматизировано 200 рабочих мест. Команда проекта со стороны исполнителя составила 7 человек, также были сформированы рабочие группы со стороны заводов и торгового дома холдинга «РМ-Терекс».
Уникальность проекта состоит в обширной номенклатуре деталей машин: более 8000 деталей и сборочных единиц в составе готовой продукции. Ещё одной особенностью проекта является реализация полноценного обмена с PDM-системой с автоматическим формированием справочника «Ресурсные спецификации» (более 10 000 ресурсных спецификаций).
Для оперативного планирования и перепланирования производственной программы реализован дополнительный модуль. Для производственной программы на месяц формируется более 45 000 этапов производства.
Особенностью проекта является последовательный переход на новую ИТ-архитектуру. Было принято решение реализовать переход в два этапа, что потребовало реализации промежуточных интеграционных обменов между новой и старой системами.
сокращены НЗП и складские запасы
сокращён производственный цикл
повышена точность планирования
увеличена скорость обработки заказов
Создание комплексной системы управления деятельностью компании «РМ-Терекс» позволило отказаться от работы в разрозненных информационных системах, выстроить работу торгового дома, дилеров и производственных площадок. Для специалистов отделов закупок и логистики система стала важнейшим инструментом обеспечения краткосрочных и долгосрочных потребностей, в том числе консолидированных по заводам. Выстроено взаимодействие между диллерами, торговым домом и заводами. Повышено качество взаимодействия между торговым домом и производственными площадками. Повышена скорость обработки заказов клиентов. Также проведена нормализация производственной НСИ на «Тверском экскаваторе».
Результатами проекта стали следующие показатели:
- сокращение НЗП и складских запасов — до 10%;
- сокращение производственного цикла — до 5%;
- повышение точность планирования — до 25%;
- увеличение скорости обработки заказов — до 25%.
В будущем планируется развитие функционала системы в части управления в области продаж, маркетинга, анализа работы департаментов.