«Судостроительный завод „Вымпел”» построил систему автоматизированного управления, которая учитывает особенности судостроительной отрасли. В системе используются прикладные решения «1С:Управление производственным предприятием 1.3» и «1С:Документооборот». В несколько раз сокращено время расчёта плановой сметы для нового проекта заказчика. Также в два раза сократилось время подготовки производства.

«Судостроительный завод „Вымпел”» — динамично развивающаяся компания, специализирующаяся на выпуске средне- и малотоннажных морских и речных судов и катеров военного и гражданского назначения. С момента основания в 1930 году на предприятии выпущено свыше 30 тысяч кораблей различных типов.
Цели:
- повышение качества и эффективности управления вследствие увеличения скорости получения необходимых данных;
- получение оперативной информации о жизненном цикле документов и изделии: его состоянии, проценте выполнения и временных и материальных затрат;
- повышение производительности и эффективности труда работников подразделений предприятия.
Доклад Александра Громцева на бизнес-форуме 1С:ERP
Задачи проекта:
- комплексная автоматизация производства, его планирования и формирования план-фактного анализа затрат;
- обеспечение высокой скорости доступа к необходимой информации, качества и достоверности её предоставления, оперативности изменения;
- повышение достоверности информации и документации, а также устранение ошибок при их обработке и учёте;
- исключение прохождения документов в бумажном варианте; их создание, изменение содержания, состояния и закрытие в электронном виде;
- минимизация влияния человеческого фактора;
- сокращение временных и трудозатрат на создание первичной документации;
- невозможность обхода «узких мест» заинтересованными лицами;
- разграничение прав доступа к информации, участвующей в данных бизнес-процессах.
Автоматизация «Судостроительного завода „Вымпел”» началась давно, одним из первых решений стала собственная уникальная разработка на FoxPro, которая позволяла строить упрощённый график производства по проекту и выписывать электронные заказ-наряды. Позже была автоматизирована бухгалтерия предприятия на системе «1С:Бухгалтерия 7.7».
Однако график планирования на календарный год формировался по укрупнённым этапам в MS Project Expert. Соответственно, говорить о привязке этапов к конкретным работам, технологической и конструкторской документации, кадровому составу, складским остаткам не приходилось, информация существовала в разрозненном виде. Расчёт себестоимости будущего заказа выполнялся вручную в Excel. Процесс выписки подразделениями предприятия документов «Требование — накладная» вёлся вручную по устаревшим, неоткорректированным материальным и заказным ведомостям.
Качественные изменения в сфере информационных технологий произошли в тот момент, когда было принято решение о комплексной автоматизации завода на базе программного продукта «1С:Управление производственным предприятием 1.3». Проект выполнялся с января по октябрь 2015 года. Первым шагом стала доработка автоматизации обмена между системой «1С:Управление производственным предприятием 1.3» и PLM-системой. Вторым шагом был реализован функционал комплексной автоматизации производства и план-фактного анализа затрат.
ИТ-архитектура завода
Современный информационный ландшафт «Судостроительного завода „Вымпел”» показан на рис. 1.
Рис. 1. ИТ-ландшафт «Судостроительного завода „Вымпел”».
- Конструирование судна ведётся в программных средах «Компас 3D», SolidWorks, AVEVA MARINE.
- В качестве системы управления конструкторско-технологической документацией (PLM) используется система «Лоцман:PLM».
- Планирование производственных работ на верхнем (межцеховом) уровне ведётся частично в специализированной системе управления строительством судна AVEVA MARS, частично в системе «1С:Управление производственным предприятием 1.3».
- Внутрицеховое планирование и фактический учёт ведётся в системе «1С:Управление производственным предприятием 1.3». Там же производится финансовое планирование, ведётся план-фактный анализ, управление закупками и расчёт себестоимости.
- Для согласования документов используется система «1С:Документооборот».
Все системы тесно интегрированы друг с другом. Обмен между системой «1С:Управление производственным предприятием 1.3» и PLM-системой происходит два раза в сутки по трём потокам.
Отметим, что, так как задачи судостроения достаточно специфичны и сложны, типовую систему «1С:Управление производственным предприятием 1.3» серьёзно модифицировали, объём уникальных доработок измерялся тысячами часов работы разработчиков. Автоматизировано 277 рабочих мест.
Разбивка судна на техкомплекты — это творческий процесс, где нет жестких правил, поэтому его результат сильно зависит от квалификации исполнителя и его опыта. Планирование изготовления техкомплектов должно быть подчинено определённому глобальному графику работ, чтобы не было простоев, а также затоваривания складов и производственных площадей.
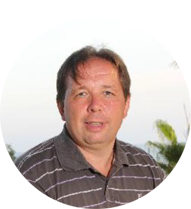
Существенный объём доработок потребовался для создания контрольных точек и специализированных задач:
- контроль план-факта выполнения работ по техкомплектам и планово-учётным единицам;
- контроль обеспечения техкомплектов материалами;
- контроль потребления материалов производством;
- привязка закупки к позициям из производимых техкомплектов (планово-учётных единиц), а также отражение графика поступления товарно-материальных ценностей и график оплат;
- предварительный расчёт цены будущего заказа.
«Судостроительный завод „Вымпел”» получил инструмент управления, который работает с учётом особенностей судостроительной отрасли: высокая степень неопределённости в момент старта проекта в работу, длительный цикл изготовления изделия, большой масштаб работ.
Основные качественные результаты:
- Значительно выросла исполнительская дисциплина: контроль работ теперь ведется одновременно по нескольким параметрам — по готовности изделия, по объёму потраченных материалов, по объёму выполненных работ, по данным ОТК.
- Отслеживается целевое использование материалов и денежных средств — от момента возникновения потребности, до фактической их траты.
- Оперативно отслеживаются контрольные точки прохождения проекта.
Количественные результаты:
- в несколько раз сокращено время расчёта плановой сметы для нового проекта заказчика, предприятие теперь может быстро обрабатывать запросы новых заказчиков;
- также в два раза сократилось время подготовки производства.